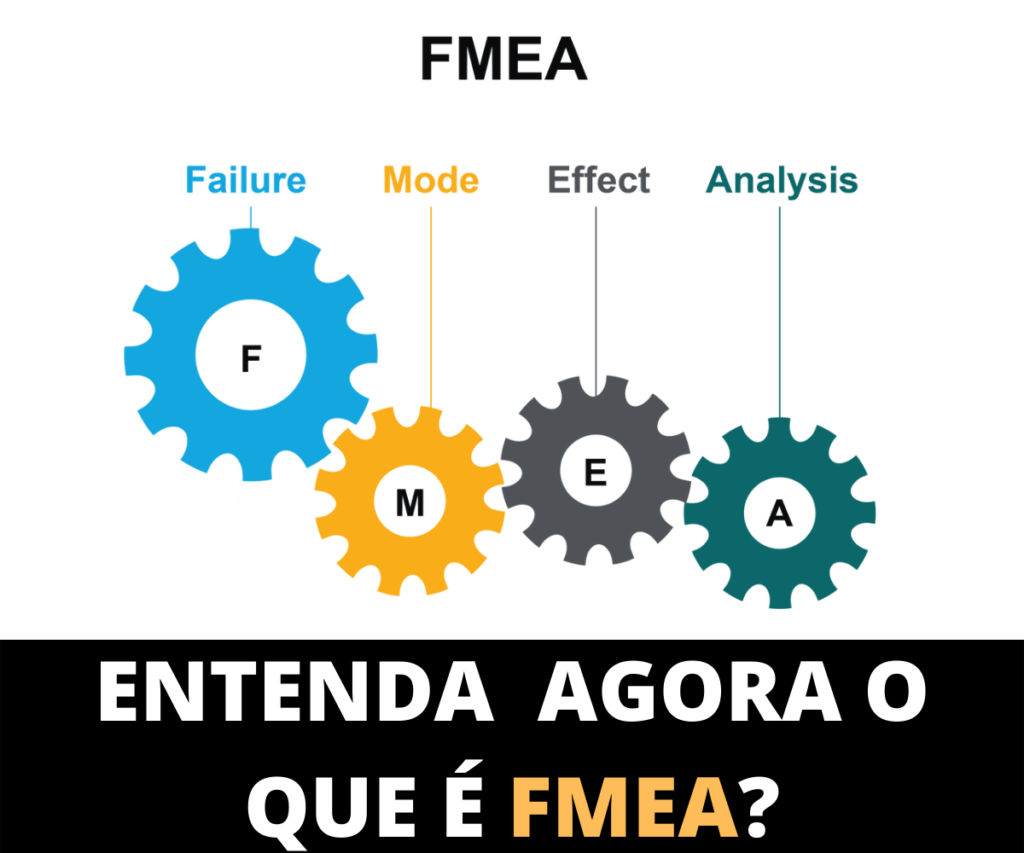
FMEA
A sigla FMEA significa Failure Mode and Effect Analysis, ou em português, Análise de Modos de Falha e seus Efeitos.
É uma técnica que possibilita analisarmos possíveis falhas de processos ou produtos mostrando o que suas ocorrências poderiam causar.
Desta forma, é possível identificar ações e melhorias para evitar ou amenizar a falha e seus efeitos.
Tem como principal objetivo estudar e analisar as falhas, tornando o processo, ativo ou produto mais confiável.
Surgiu em meados da década de 40 onde foi utilizado em operações militares para avaliar confiabilidade de sistemas e equipamentos. Atualmente é muito utilizada em diversas áreas contribuindo para garantir a segurança e eficiência.
Tipos de FMEA
O FMEA pode ser aplicado e adaptado em diversas funções e áreas especificas.
Os mais conhecidos…
FMEA de Produto: Também conhecido como FMEA de Projeto é aplicado sobre as falhas de produto ou projeto novo ou já existente.
FMEA de Processos: Aplicado sobre as falhas de processo novo ou já existente.
Apresentação
Em geral o FMEA é apresentado em forma de uma planilha, onde se reúnem todas as possíveis falhas, causas e efeitos do produto, processo ou ativo.
FMEA na prática
Basicamente o FMEA pode ocorrer da seguinte forma:
1 – Montar equipe
O time responsável pelo estudo dever ser composto por profissionais de diversas áreas envolvidas. Desta forma será possível ter diversas formas de enxergar as falhas e seus impactos.
2 – Identificar falhas
A equipe identifica onde e de que forma as possíveis falhas podem ocorrer.
Para facilitar o estudo das falhas costuma-se dividir o objeto de estudo (Produto, Projeto, Processo, Equipamento…) em partes, locais ou etapas.
3 – Identificar os efeitos das falhas
Após mapeado as falhas identificar os possíveis efeitos que podem ser causados.
4 – Identificar as causas da falhas
Entender o que faz a falha ocorrer, de forma a evita-la.
5 – Definição RPN
RPN é a sigla para Risk Priority Number (Número de Prioridade de Risco).
Simplesmente uma forma de atribuir importância para cada análise de falha feita e desta forma priorizar as ações.
Para cada item estudado são atribuídos pontos para severidade, ocorrência e detecção.
O RPN é a multiplicação dos pontos atribuidos para severidade, ocorrência e detecção.
6 – Plano de ação
Após todas as etapas anteriores serem feitas a equipe deverá criar um plano de ação com melhorias e ações para evitar falhas identificadas e seus efeitos.
7 – Monitoramento
Acompanhamento da execução do plano de ação, verificação da eficácia das ações e ajustes se necessário.
Gostou deste conteúdo?
Quer se especializar?
Confira este treinamento:
ESPECIALISTA EM MELHORIA CONTINUA